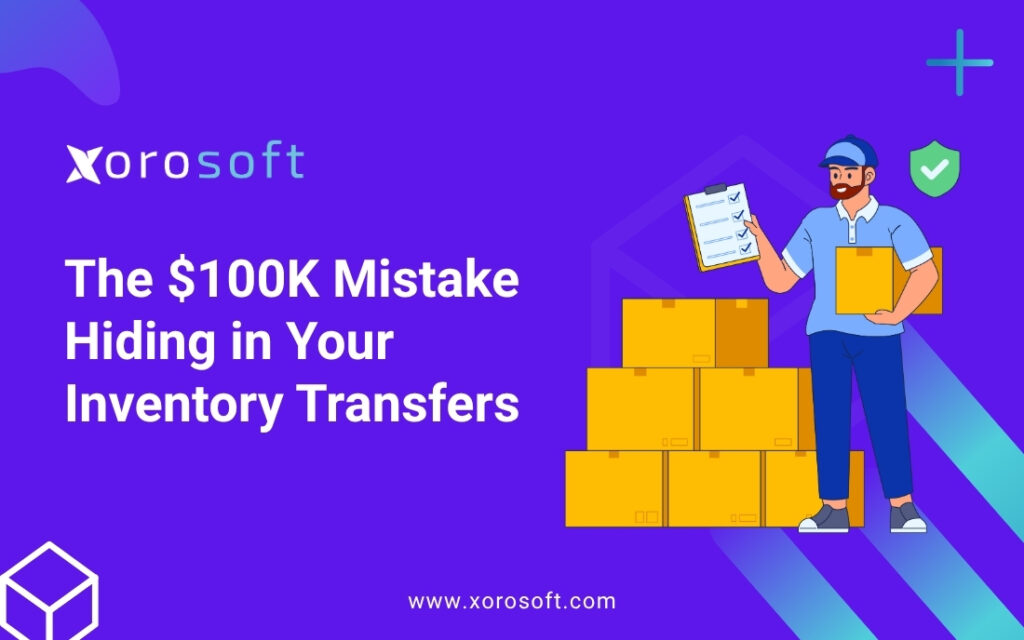
How Inventory Transfer Mistakes Drain Your Profits
Scaling a product-based business comes with big challenges—but one of the most expensive is often invisible: inventory transfer mistakes.
While most leaders focus on marketing, fulfillment, and customer growth, many overlook the routine, everyday process of moving stock between warehouses, stores, or 3PLs. Yet these transfers, when mismanaged, can result in over $100,000 in losses each year.
Surprisingly, this problem often goes unnoticed until it’s too late. As a result, companies experience revenue loss and operational chaos.
Let’s break down how these mistakes happen, why they’re so common, and how your team can eliminate them for good.
How Routine Transfers Become a Costly Risk
As your business grows, inventory is constantly on the move. Products shift between locations daily—warehouse to warehouse, store to store, or even from suppliers to fulfillment centers.
However, most companies don’t have systems that track these transfers in real time.
This leads to:
-
Inventory marked as shipped, but never received
-
Transfers logged late or not at all
-
Items stuck in “in transit” limbo
-
Discrepancies between what was sent vs. what’s received
Each of these issues contributes to inventory transfer mistakes.
Consequently, you end up with:
-
Overstock in some locations, stockouts in others
-
Tied-up capital and missed reorder points
-
Shipping delays and unhappy customers
-
Conflicts between warehouse, finance, and sales teams
Eventually, these issues add up to lost revenue, wasted resources, and constant firefighting.
The Real Reasons Your Inventory Keeps Going Missing
The root cause isn’t your people—it’s your tech stack.
Most teams rely on outdated or disconnected tools: spreadsheets, shipping apps, legacy ERPs, and separate warehouse software. Unfortunately, these systems weren’t built to talk to each other.
As a result, the entire transfer process breaks down.
-
Your ERP shows a transfer completed, but the receiving team hasn’t confirmed it
-
Warehouse apps update too slowly—or not at all
-
No one is accountable because there’s no automated tracking or approval process
-
Inventory data across systems becomes outdated and inconsistent
To make matters worse, there’s no simple way to reconcile discrepancies once they appear.
That’s why these inventory transfer mistakes become inevitable. And as your operations scale, so does the complexity.
How Smart Teams Take Control of Stock Movement
Fortunately, modern businesses are turning to cloud-native ERP systems to solve this challenge. By unifying inventory, warehouse, fulfillment, and finance into one platform, they gain control and clarity.
Here’s how they do it:
-
Live inventory updates across all warehouses, stores, and 3PL partners
-
Built-in transfer workflows with automated validations
-
Real-time data that aligns operations, accounting, and purchasing
-
Cross-platform syncing, so no step gets missed or misreported
In other words, they remove the guesswork and eliminate the need for manual follow-ups.
Moreover, with automation in place, teams can shift their focus from fixing issues to optimizing performance.
How Xorosoft Eliminates Inventory Transfer Issues
Xorosoft ERP is purpose-built to eliminate transfer errors at scale. As a result, your team can move faster, minimize errors, and operate with total accuracy.
Designed for growing manufacturers, retailers, and distributors, it centralizes your operations and fixes common pain points.
✔️ Live, Multi-Location Inventory Tracking
Whether your stock is in a warehouse, store, truck, or 3PL facility, you’ll always know exactly where it is—and how much you have. No lag. No confusion.
✔️ Built-In WMS for Real-Time Transfer Accuracy
Xorosoft includes a full-featured WMS that tracks every transfer, validates data, and syncs instantly with your inventory system.
Therefore, your team avoids the hassle of mismatched entries or delayed updates.
✔️ Smart Automation to Prevent Errors
Configure automatic rules for frequent or recurring transfers. In turn, you reduce manual updates, lower human error, and improve efficiency.
✔️ Seamless Integration with Your Tech Stack
Xorosoft connects directly with platforms like Shopify, Amazon, EDI, and 3PLs—ensuring inventory moves are reflected everywhere instantly.
As a result, you maintain visibility from end to end without extra work.
✔️ Ranked #1 in Ease of Use on G2
Ranked #1 in Ease of Use on G2, Xorosoft helps your team adopt it quickly. There’s no need for lengthy training or technical overhead.
✔️ Actionable Reports to Stay Ahead
You’ll gain access to dashboards that highlight transfer issues, shrinkage, and bottlenecks. Consequently, you can make proactive decisions based on accurate, real-time data.
Save Money by Fixing Transfer Gaps Before They Scale
Ignoring inventory transfers comes at a price. If you’re still using spreadsheets or siloed tools, these are the results you’ll likely face:
-
Constant surprises when stock “vanishes”
-
Wasted cash on emergency reorders or overstock
-
Finance teams chasing operations for clarity
-
Customer frustration due to inaccurate availability
Even though each issue seems small, together they add up to massive inefficiencies.
But here’s the good news: all of this is preventable.
Don’t Let Inventory Transfer Mistakes Cost You Another Dollar
When your inventory transfers are automated, auditable, and reliable, your entire operation becomes more efficient.
With Xorosoft ERP, you can:
-
Prevent costly inventory transfer mistakes
-
Reduce manual work and team frustration
-
Gain real-time clarity into all your stock movements
-
Scale confidently—without sacrificing control
👉 Book a free demo today and see how Xorosoft can transform your operations and bottom line.