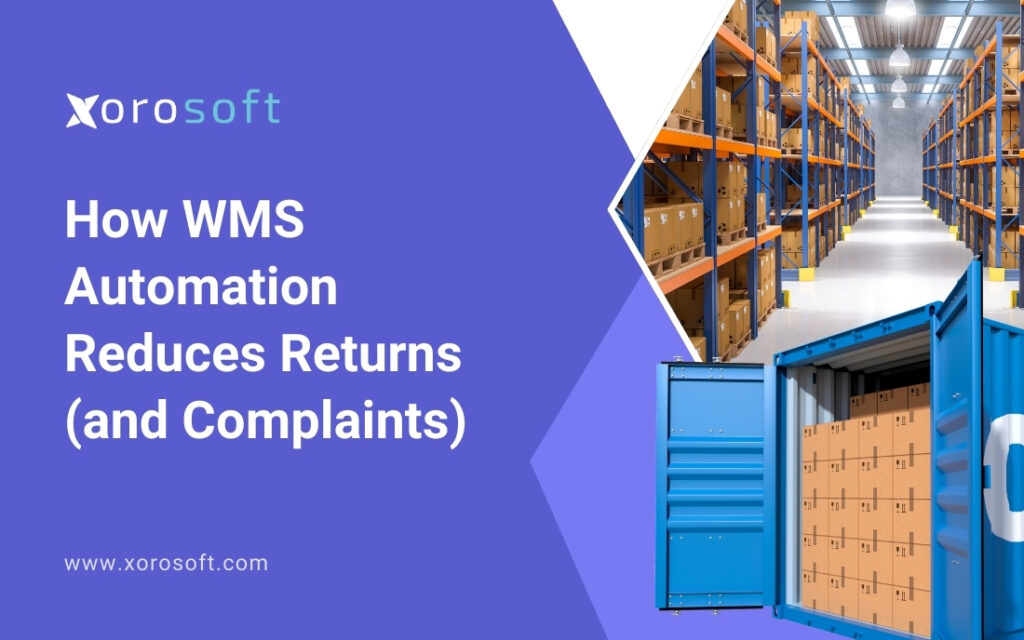
WMS Automation Helps You Avoid Unnecessary Returns
WMS automation is the key to reducing product returns and keeping customers happy.
Every return doesn’t just mean lost revenue—it means lost trust.
Most returns aren’t due to poor products. They happen because of mistakes in fulfillment: sending the wrong item, missing delivery windows, or poor inventory visibility.
As your business grows, even small mistakes can have a big impact. That’s why automation in your warehouse matters more than ever.
Small Fulfillment Errors Lead to Big Problems
In many cases, returns start with avoidable errors inside your warehouse. These problems often look like:
-
Picking the wrong item
-
Inventory not updated in real time
-
Manual labels causing duplicate shipments
-
Slow return processing that frustrates customers
As a result, returns increase, support tickets pile up, and customer satisfaction drops.
These issues can hold your business back—especially when they happen repeatedly.
Disconnected Systems Are a Silent Killer
Many growing businesses use multiple tools that don’t work together.
For example, Shopify for online sales, QuickBooks for accounting, a separate app for shipping, and spreadsheets for returns.
This disjointed setup creates major challenges:
-
No live view of inventory
-
No barcode checks during packing
-
No system to manage returns properly
-
No clear link between teams or departments
As a result, fulfillment becomes a guessing game. Customers feel the impact—and they respond with returns and complaints.
A Smarter Way to Run Your Warehouse
There’s a better way.
When your business uses a warehouse management system that’s automated and integrated, everything changes for the better.
With WMS automation in place, you’ll benefit from:
-
Real-time stock updates across all warehouse locations
-
Barcode scanning to prevent mis-picks and mis-packs
-
Guided workflows that help your team move faster
-
Automated returns that restock items accurately
This means fewer errors and faster processes. Most importantly, customers get what they ordered, on time, and without issues.
What Makes Xorosoft’s WMS Automation Different
Xorosoft is not just another ERP. It’s a cloud-based, all-in-one platform with a fully built-in WMS.
This means your warehouse operations are connected to your inventory, accounting, sales, and procurement—all in real time.
Here’s how Xorosoft helps reduce returns:
-
Bin-level management that maps products to the right locations
-
Barcode-driven scanning that ensures accuracy
-
Real-time syncing with platforms like Shopify, Amazon, and EDI
-
Instant return-to-stock updates with full traceability
-
Live dashboards that track every warehouse action
In contrast to bolt-on systems, Xorosoft’s WMS is part of the core ERP.
That’s why businesses see better accuracy, faster fulfillment, and fewer returns.
We’re also rated #1 for Ease of Use on G2 and available in the Shopify App Store for easy integration.
What Real Businesses Experience After Switching
Companies that adopt Xorosoft’s WMS automation see:
-
Up to 60% fewer product returns
-
Major drops in mis-picks and late shipments
-
Faster inventory reconciliation after returns
-
Happier customers and higher review scores
This means your operations can grow—without growing pains.
Ready to Reduce Returns and Complaints?
Returns will happen. But when your warehouse is disorganized, they happen more often—and cost more than they should.
WMS automation from Xorosoft helps you fix the problem at the source.
By streamlining fulfillment and syncing every part of your operations, you can:
-
Cut down on returns
-
Speed up order handling
-
Keep your customers satisfied
Explore Xorosoft or book a free demo to see how smarter warehousing can change everything.