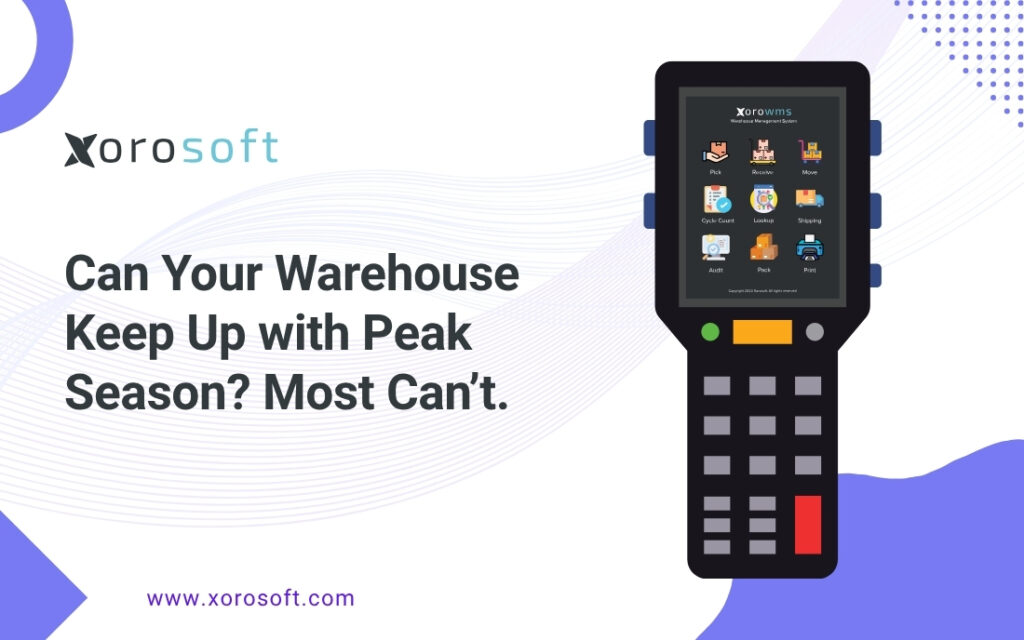
Peak Season Exposes Weaknesses in Warehouse Management
Let’s be real—peak season isn’t the time to discover flaws in your system.
If your warehouse management during peak season relies on duct-taped tools, slow updates, and manual processes, you’re heading straight into trouble.
Every year, companies brace for high demand—Black Friday, holiday sales, new product drops. While sales spike, so do fulfillment issues. Teams scramble, shipments delay, and customer satisfaction takes a nosedive.
But the real question is this:
Can your warehouse handle it—or will it break under pressure?
Common Breakdowns in Warehouse Management During Peak Season
Peak season puts every flaw under a magnifying glass.
If your workflows are inefficient, they will crumble fast. If your systems aren’t connected, they’ll slow you down.
Here’s what typically goes wrong:
-
Inventory numbers become unreliable. Your system claims 150 units in stock, but there are only 140—or worse, none.
-
Order picking gets chaotic. Workers zigzag across the floor instead of following optimized paths.
-
Shipping falls behind. Fulfillment can’t keep up, causing missed deadlines and missed revenue.
-
Customer complaints pile up. Even one delayed package can snowball into negative reviews and churn.
These aren’t isolated issues. They’re signs that your warehouse management during peak season is stretched too thin by outdated tools.
The Real Problem: Disconnected Systems and Delayed Information
Many businesses still rely on a scattered tech stack—spreadsheets for inventory, shipping apps for fulfillment, QuickBooks for accounting, and maybe a basic WMS tacked onto a legacy ERP.
This disconnected setup creates two critical problems:
Data Delays That Kill Agility
When systems don’t update in real-time, you’re always a step behind.
By the time you realize you’re low on a hot product, you’ve already sold out—and disappointed multiple customers.
In contrast, live data enables faster decisions and proactive inventory management during peak season.
Operational Silos That Slow Teams Down
Sales, warehouse, and finance all use different tools.
Because of this, sales doesn’t see real stock levels. Warehouse staff doesn’t know which orders are urgent. Finance ends up reconciling chaos after the fact.
This lack of alignment creates slowdowns, miscommunication, and tension across teams—right when speed matters most.
How Centralized ERP Systems Solve Peak Season Bottlenecks
To fix warehouse management during peak season, you need a system that keeps your entire business in sync.
That’s where a centralized ERP with a built-in warehouse management system (WMS) comes in. It doesn’t just track stock—it orchestrates every part of your operation, from procurement to fulfillment to accounting.
Here’s what you gain from making the switch:
-
Inventory is tracked in real time, even across multiple warehouses.
-
Picking routes are optimized automatically, improving speed and accuracy.
-
Low-stock alerts and automated purchase orders keep items flowing.
-
Orders from Shopify or Amazon flow straight into your system—no manual entry required.
-
Finance and warehouse teams access the same data, in real time.
All of this works together to keep your warehouse running smoothly—even when demand surges.
How Xorosoft ERP Improves Warehouse Management During Peak Season
At Xorosoft, we designed our ERP with warehouse management during peak season in mind.
It’s a modern, cloud-native system with a deeply integrated WMS—not an afterthought. Let’s look at how it transforms warehouse operations.
Real-Time Inventory Control You Can Trust
Xorosoft tracks your inventory down to the bin level—across all locations.
With real-time visibility, you can manage stock confidently, reduce shrinkage, and avoid overselling.
In addition, our platform supports multi-location, multi-currency, and multi-channel operations—so you can scale with clarity, not confusion.
Automation That Eliminates Repetitive Tasks
Why waste time manually reordering items or generating shipping labels?
With Xorosoft, you can automate reorder points, barcode scanning, label creation, and warehouse task assignments.
That means your team stays focused on shipping, not clicking.
This kind of automation becomes invaluable when warehouse demand surges, especially during seasonal peaks.
Seamless Integration with E-Commerce Platforms
Xorosoft integrates natively with Shopify, Amazon, EDI, and 3PLs. Your orders sync in real time, without the need for third-party tools or manual updates.
👉 Try it out via the Xorosoft Shopify App
This ensures warehouse operations begin the moment a customer checks out—no gaps, no guesswork.
Fast Deployment and Cloud Flexibility
While traditional ERPs take months to roll out, Xorosoft can be deployed fast.
Its cloud-native architecture also means real-time updates and secure access from anywhere—especially useful for hybrid or remote teams managing multi-location warehouses.
On top of that, Xorosoft is ranked #1 in Ease of Use on G2.
👉 Read the reviews here:
https://www.g2.com/categories/erp-systems?rank=1&tab=easiest_to_use#rank-1
Built-In Dashboards for Smarter Decision-Making
During peak season, every second counts.
Xorosoft gives you visual dashboards and reports that track order flow, fulfillment rates, revenue, and delays in real time.
Instead of relying on post-mortem reports, you get a live pulse on performance—so you can adjust before problems snowball.
What Peak Season Looks Like with the Right Tools
When your warehouse management during peak season runs through Xorosoft ERP, your business gains speed, visibility, and control.
That means:
-
Customers get their orders on time
-
Warehouse teams move faster, with fewer errors
-
Finance gets real-time numbers, not end-of-month surprises
-
You scale without stress
In short, you stop surviving peak season—and start mastering it.
📦 Ready to optimize your warehouse before the next surge?
👉 Book your free Xorosoft demo