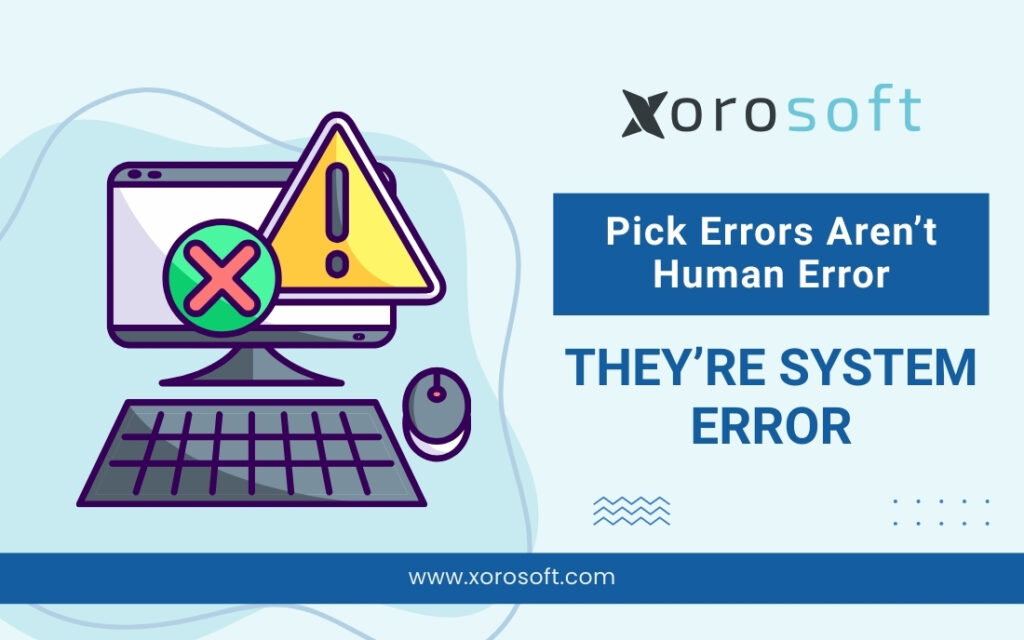
When the Wrong Box Shows Up, It’s Not Your Team’s Fault
Ever had a customer call to say they received the wrong item—and your gut reaction was to blame the picker? That’s what most businesses do. But here’s the truth: your team isn’t the problem. Your systems are.
In fast-paced warehouses, humans aren’t failing. They’re working with tools that are stuck in the past—manual pick lists, clunky software, outdated integrations. If your operations feel like a game of “guess and check,” it’s not because your staff can’t handle the job. It’s because your tech can’t handle the scale.
The Operational Domino Effect
When systems break down, people make mistakes. And in the warehouse, even a small error—like picking the wrong variant—can snowball:
-
Orders delayed or returned
-
Inventory thrown out of sync
-
Extra labor to correct the issue
-
Customer satisfaction drops
Most of this chaos stems from outdated or disconnected tools:
-
Orders come in from Shopify or Amazon, but don’t update your system in real time
-
Inventory shows as available, but it’s not actually in the right bin
-
Paper pick lists get lost or misread
-
Your ERP doesn’t validate barcodes—or doesn’t even support scanning
These aren’t human errors. They’re system failures dressed up as operator mistakes.
The Core Problem: Disconnected and Outdated Systems
Warehouses today run like the backend of an e-commerce engine. You can’t afford guesswork or manual processes.
But when your ERP system isn’t designed for warehouse logic—zone picking, barcode validation, real-time bin updates—you’re essentially flying blind.
Disconnected platforms, patchwork integrations, and legacy systems can’t keep up with the speed of modern fulfillment. So your team ends up working harder just to stay afloat.
The Smart Fix: A System Built to Prevent Mistakes
Here’s the fix: a modern ERP system with a built-in WMS that doesn’t just track inventory—it drives your entire warehouse operation.
With a connected ERP and WMS, you get:
-
Real-time inventory accuracy across all channels and bins
-
Guided digital picking that tells your team what to grab, where, and when
-
Barcode validation that catches errors before they ship
-
Instant order sync with Shopify, Amazon, 3PLs, and more
-
Data dashboards that show where delays or errors are happening
This isn’t about micromanaging your team—it’s about finally giving them the tools they need to do their job right, the first time.
Why Xorosoft ERP Changes the Game
At Xorosoft, we built an ERP system that doesn’t bolt warehouse tools on as an afterthought—it’s engineered for scale from the ground up.
Here’s how we help:
-
Native warehouse management system—no third-party plugin mess
-
Shopify + Amazon integration with real-time order and stock updates
-
Automated fulfillment logic—pick, pack, route, repeat
-
Smart barcode scanning to eliminate mis-picks
-
Multi-location and multi-currency support
-
Fast deployment so you’re not waiting months to go live
-
Ranked #1 for Ease of Use on G2
-
Live now on the Shopify App Store
Xorosoft doesn’t just help you ship faster. It helps you stop losing money on preventable errors.
Ready to Stop Playing the Blame Game?
If your team is spending more time fixing mistakes than fulfilling orders, the problem isn’t effort. It’s architecture.
Stop blaming people for system failures. Start equipping them with tech that doesn’t break under pressure.
👉 Explore Xorosoft ERP or Book a demo today. Give your team tools that actually work—and watch what happens.
Search
Categories
- ACCOUNTING & FINANCIALS 41
- Business 1
- E-COMMERCE & CHANNEL INTEGRATIONS 50
- ECommerce 3
- ERP 711
- FINANCE & ACCOUNTING 9
- INVENTORY & OPERATIONS 11
- Inventory Management Software 1
- OPERATIONS & INVENTORY 41
- PROCUREMENT & SUPPLY CHAIN 9
- PURCHASING & SUPPLY CHAIN 42
- Software 1
- WAREHOUSE & FULFILLMENT WMS 43
- WMS & FULFILLMENT 12