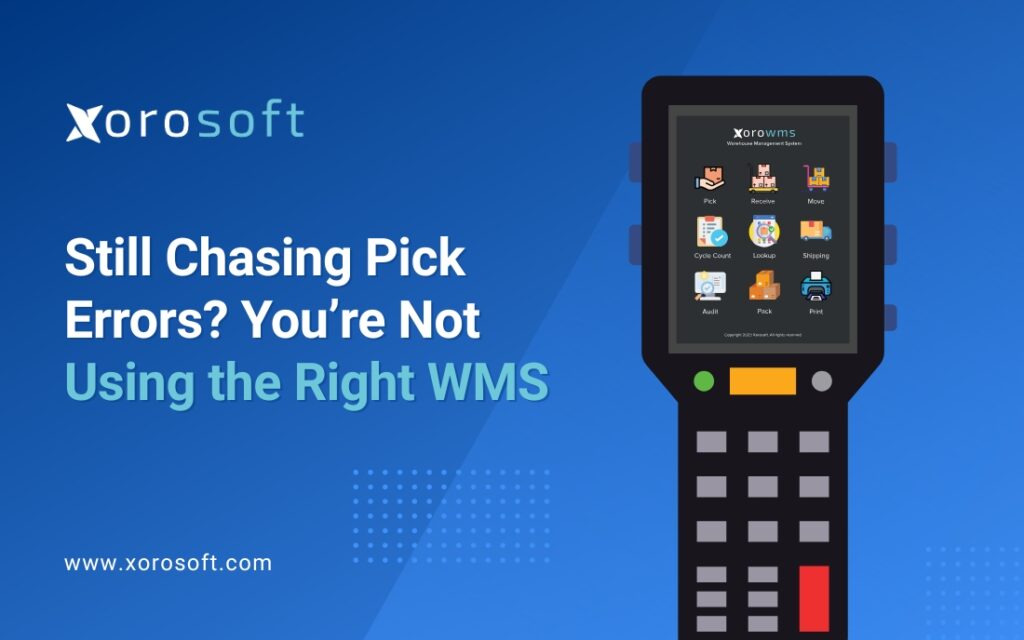
Pick Error Reduction Is No Longer Optional
Pick error reduction is no longer optional—it’s mission critical.
If you’re still chasing mistakes in your warehouse, it’s time to re-evaluate your tools. Every time a customer gets the wrong item—or doesn’t get their order at all—someone scrambles to fix it. A rep logs a ticket. The warehouse checks inventory. The cycle never ends.
The frustrating part? Your team is probably working hard. However, they’re stuck fighting a system that isn’t built for speed or accuracy. And that’s the real problem.
How Pick Errors Are Hurting Your Bottom Line
Pick errors seem like small problems—until they pile up.
-
Orders get delayed or repacked
-
Refunds and reships eat into your profit
-
Customer complaints escalate, damaging loyalty
-
Inventory becomes unreliable, which requires constant recounts
As your order volume scales across Shopify, Amazon, or wholesale, these issues multiply. Consequently, what used to be manageable becomes a daily operational nightmare. More importantly, it stops your team from focusing on what really matters: growth.
That’s why smart businesses shift focus to proactive pick error reduction strategies—driven by the right technology. Additionally, reducing errors helps you build lasting customer trust.
The Real Reason Pick Errors Keep Happening
Let’s be honest: no one wants to make mistakes at work. Yet many companies still blame warehouse staff.
In reality, most pick errors occur because of outdated systems and disconnected workflows. For example:
-
Inventory updates aren’t in real time
-
Shopify, Amazon, and B2B channels don’t sync
-
Teams rely on printed pick sheets instead of scanners
-
The WMS is a clunky bolt-on
-
No smart routing causes confusion and wasted time
Therefore, even skilled employees make avoidable mistakes. The core issue isn’t a lack of effort—it’s a lack of system support. Until your process prevents errors by design, you’ll always be in catch-up mode.
Moreover, poor visibility creates bottlenecks across the entire operation. As a result, even minor errors trigger large-scale inefficiencies. For this reason, system design becomes critical.
What Real Pick Error Reduction Looks Like
Fortunately, there’s a better way forward. Cloud-native warehouse systems now reduce errors proactively—not just reactively.
Here’s what best-in-class WMS platforms offer to ensure pick error reduction:
-
Barcode validation so only the correct item gets picked
-
Live inventory tracking that’s accurate across all channels
-
Smart pick lists and guided routing to prevent confusion
-
Replenishment alerts before stockouts can occur
-
Seamless integration with Shopify, Amazon, EDI, and 3PLs
As a result, companies using these systems consistently report 99.9% picking accuracy. Instead of fixing errors, they prevent them.
In addition, automation allows teams to focus on high-value work. Furthermore, when your systems are in sync, fulfillment becomes smoother. Therefore, the shift isn’t just technical—it’s strategic.
Likewise, improved workflows reduce training time and improve staff morale. Above all, consistent performance becomes your new standard.
How Xorosoft Helps Eliminate Pick Errors
At Xorosoft, we designed our ERP differently. It includes a fully integrated WMS, rather than relying on disconnected tools or bolt-on apps.
Here’s how Xorosoft drives consistent pick error reduction:
-
Barcode scanning verifies each item at the source
-
Real-time inventory provides accurate stock levels
-
Smart pick routing and wave picking streamline warehouse flow
-
Multi-location visibility ensures consistency across all sites
-
Live dashboards and alerts help managers stay proactive
-
Built-in integrations keep everything from Shopify to Amazon synced
In addition, Xorosoft doesn’t require weeks of training. It’s simple by design. In fact, Xorosoft is ranked #1 in Ease of Use on G2 and available on the Shopify App Store as a fully integrated ERP.
Not only is it powerful, but it’s also intuitive. As a result, your team adapts faster, and you gain value sooner. Similarly, you don’t need an IT team to manage it.
Consequently, businesses experience fewer delays and fewer returns. Because the platform operates in real time, everything stays aligned.
Take Control of Pick Accuracy—Before It Hurts Growth
You can’t grow your business on systems that let avoidable mistakes slip through. With Xorosoft ERP, you reduce pick errors from day one.
Because the system is designed to catch issues before they escalate, your team spends more time scaling and less time troubleshooting.
Fewer mistakes. Faster fulfillment. Happier customers.
Search
Categories
- ACCOUNTING & FINANCIALS 40
- Business 1
- E-COMMERCE & CHANNEL INTEGRATIONS 50
- ECommerce 3
- ERP 709
- FINANCE & ACCOUNTING 9
- INVENTORY & OPERATIONS 11
- Inventory Management Software 1
- OPERATIONS & INVENTORY 41
- PROCUREMENT & SUPPLY CHAIN 9
- PURCHASING & SUPPLY CHAIN 41
- Software 1
- WAREHOUSE & FULFILLMENT WMS 43
- WMS & FULFILLMENT 12