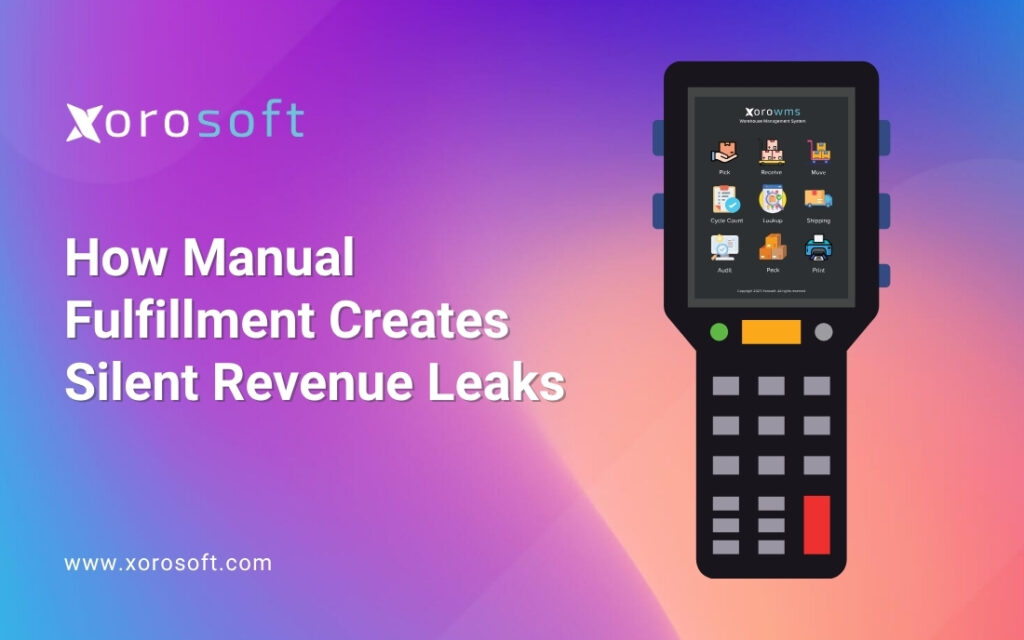
The Hidden Cost of Manual Fulfillment Errors in Scaling Businesses
Manual fulfillment errors are one of the most overlooked problems in scaling operations. You’re shipping hundreds—maybe thousands—of orders a month. Your team is hustling. Spreadsheets are flying. Labels are printing. But somehow, profits aren’t where they should be.
The reason? You’re likely dealing with fulfillment issues—and you might not even know it.
Although these errors seem minor—like entering tracking numbers or double-checking inventory—they quietly eat away at your margins. Worse yet, they multiply as your business grows. As a result, seemingly small inefficiencies become serious leaks.
Let’s break down why this happens—and how to fix it before it drains more revenue.
The True Business Impact of Fulfillment Errors
For fast-scaling businesses—especially manufacturers, distributors, and retailers—fulfillment often feels like a fire drill.
Orders spike. Staff scramble. Inventory counts don’t match. Packages are delayed. Consequently, customers complain. Refunds go out.
Meanwhile, accounting lags behind, and reports don’t line up. Even worse, these disruptions start to feel normal.
As a result, most teams are too busy putting out fires to notice the deeper problem:
-
Revenue is lost due to mispicks and delays
-
Labor costs are inflated from repetitive manual work
-
Chargebacks and returns rise from incorrect orders
-
Inventory write-offs grow from poor tracking
-
Customers leave because delivery experiences fail
In short, manual fulfillment errors are silently damaging your bottom line. More importantly, they’re holding back your growth.
Why Manual Workflows Break at Scale
Disconnected tools, human errors, and delays start stacking up fast. Let’s break it down.
Disconnected Tools Multiply Mistakes
Many businesses rely on patched-together systems. You might use one app for orders, another for inventory, and a third for shipping.
However, these tools often don’t sync in real time. As a result, you deal with data silos, double-entry, and frequent errors.
Eventually, even small issues become big ones. Thus, what once worked no longer does.
Furthermore, your team spends more time reconciling errors than moving forward.
Lack of Inventory Visibility Leads to Wrong Picks
Without up-to-date inventory across locations, your team either oversells or undersells.
For example, a team member might pick an item that’s already out of stock at another location. This results in delays, refunds, or customer churn. Therefore, lack of visibility becomes a profit killer.
In addition, these errors often go unnoticed until customers complain—by then, it’s too late.
The Hidden Risks of Manual Fulfillment
Even if things seem manageable, manual fulfillment introduces risk across every layer of ops.
Pressure-Driven Environments Breed Errors
In busy fulfillment environments, mistakes happen fast.
Someone grabs the wrong SKU, prints the wrong label, or misses an order update. Each small mistake adds up to lost time and money. Consequently, customer trust takes a hit.
Meanwhile, your staff may feel overwhelmed or burned out. Even so, the orders keep coming.
Additionally, team morale drops when problems keep repeating. To make matters worse, error rates compound over time.
Delayed Reporting Blocks Better Decisions
Manual workflows make reporting slow and inaccurate. That leaves leadership reacting to issues instead of preventing them.
Moreover, trends go unnoticed until they’ve already affected revenue. In other words, you lose the ability to plan.
At the same time, financial forecasting becomes guesswork. Ultimately, you’re stuck in reactive mode.
What Scalable Fulfillment Should Look Like
Today’s growing businesses need more than spreadsheets and shipping apps.
They need real-time visibility, seamless automation, and integrated workflows across inventory, fulfillment, accounting, and reporting.
That’s exactly what a modern ERP provides.
With a unified ERP system:
-
Inventory updates automatically across locations and channels
-
Orders sync live between Shopify, Amazon, and your warehouse
-
Warehouse teams follow guided workflows for picking and packing
Where Fulfillment Speed Meets Financial Accuracy
-
Shipping and tracking are automated—no retyping or manual updates
-
Financials stay aligned with operations in real time
Because of this, modern ERP systems eliminate manual fulfillment errors and allow you to scale efficiently.
In contrast to outdated methods, this unified approach improves speed, accuracy, and profit.
How Xorosoft Solves Fulfillment Chaos
Xorosoft ERP is built for fast-scaling businesses that are ready to eliminate operational leaks caused by outdated tools.
Here’s how Xorosoft helps you fix fulfillment—permanently.
Real-Time Inventory and Order Sync Prevents Mistakes
Xorosoft’s cloud-native ERP updates every item and every order in real time. This keeps your entire team on the same page.
No lag. No confusion. And definitely no blind spots.
You can explore this feature in detail on our Features page.
As a result, you avoid inventory errors before they ever reach your customer.
Built-In Warehouse Management System (WMS)
Unlike bolt-on apps, Xorosoft includes a fully integrated Warehouse Management System.
With barcode scanning, bin tracking, and guided picking, your warehouse staff always know exactly what to do. As a result, accuracy improves and fulfillment speeds up.
Furthermore, onboarding new warehouse staff becomes easier and faster.
Why Real-Time Data Flow Matters More Than Ever
Xorosoft integrates natively with your tech stack, including:
-
Amazon
-
EDI
-
3PL providers
This means less switching between systems—and fewer manual fulfillment errors.
Moreover, everything stays synced across your channels without effort.
Automation from Fulfillment to Finance
Xorosoft automates your entire fulfillment process—from shipping label creation to accounting entries.
This dramatically reduces human error and speeds up your cash flow. Plus, your finance team gets accurate, real-time numbers without chasing down updates.
To illustrate, your month-end close can happen days faster.
Rated #1 for Ease of Use on G2
Xorosoft is currently ranked #1 in Ease of Use on G2 for ERP platforms.
That means your team can get up and running fast—without a steep learning curve or IT bottlenecks.
In short, it’s powerful but easy to use.
Time to Eliminate Fulfillment Mistakes for Good
Every manual task is a chance for something to go wrong. A mistyped order. A missed shipment. A lost customer.
The longer you rely on manual fulfillment, the more your margins leak—slowly and silently.
But it doesn’t have to be this way.
With Xorosoft ERP, you can:
-
Eliminate fulfillment chaos
-
Gain real-time visibility across every operation
-
Automate processes from inventory to invoicing
-
Scale confidently without bottlenecks
Ready to stop revenue leaks and run fulfillment on autopilot?
👉 Book a demo or explore Xorosoft today.