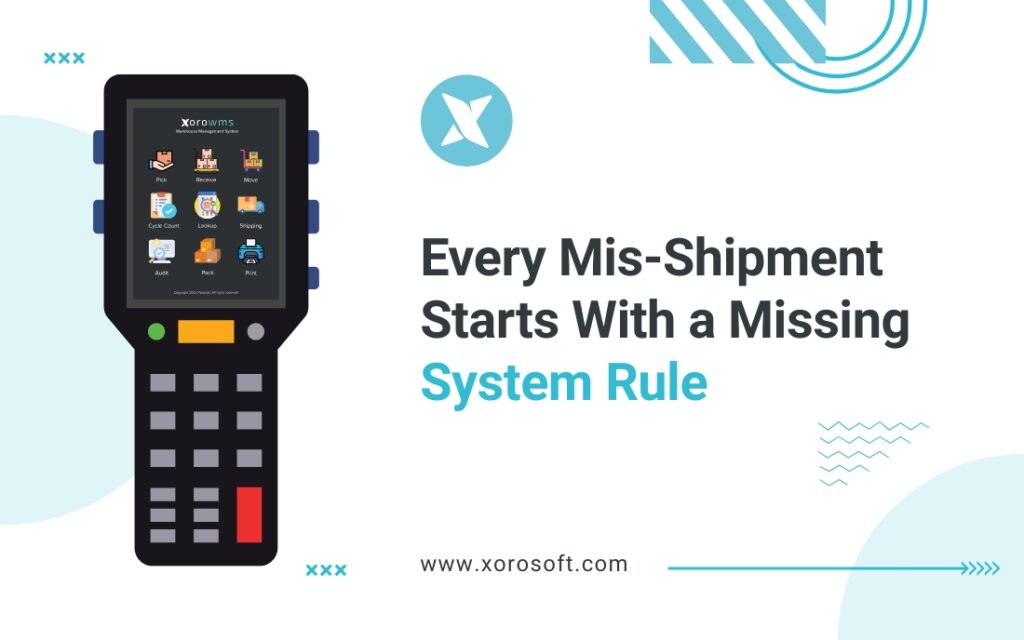
One Missing Rule Can Break Everything
Every growing business needs an ERP for inventory and fulfillment accuracy—because when that’s missing, fulfillment chaos takes over. As a result, wrong items get shipped. Eventually, orders go missing. In many cases, inventory doesn’t match what’s actually on the shelf.
These aren’t rare mistakes. In fact, they’re often the result of a system that lacks proper checks and rules. Without intelligent workflows and real-time data, small missteps spiral into costly errors. Therefore, a unified solution is essential.
What Mis-Shipments Cost Without an ERP for Inventory and Fulfillment Accuracy
Let’s be honest—fulfillment errors are expensive. And not just in terms of shipping fees.
-
Customer dissatisfaction: A single wrong item can easily push away a repeat buyer.
-
Return headaches: Processing returns drains your team’s time, energy, and profitability.
-
Inventory distortion: Each mis-shipment triggers a ripple effect across stock data.
-
Staff stress: When your team is forced to double-check everything manually, morale plummets.
These mistakes create both operational and emotional fatigue. Moreover, customers become frustrated while teams feel stuck cleaning up the mess. Consequently, growth slows down.
Why Fulfillment Errors Persist Without the Right ERP System
Blaming employees is easy, yet it misses the real issue.
Here’s what actually causes these repeat errors:
-
Disconnected tools: Inventory software doesn’t talk to shipping platforms.
-
No validation checks: Systems let orders go through with missing or incorrect data.
-
Manual dependencies: Accuracy relies too heavily on human attention.
-
No built-in logic: There’s no rule to stop shipments from warehouses with no stock.
In addition, many teams rely on spreadsheets and disjointed tools. That approach may work temporarily, but it will eventually crack under pressure. And when it does, your fulfillment performance suffers.
How an ERP for Inventory and Fulfillment Accuracy Prevents Costly Errors
Scaling operations requires more than good intentions—it needs smart infrastructure. That’s why modern ERP platforms are gaining traction.
Here’s how they help:
-
All-in-one data sync: Sales, shipping, inventory, and accounting operate from a unified system.
-
Error prevention: Smart business logic stops flawed orders before they go out.
-
Visibility: Teams can track real-time inventory, fulfillment progress, and more.
-
Automation: Repetitive steps get handled automatically, reducing manual risk.
Furthermore, this isn’t about adding complexity. On the contrary, it simplifies operations by bringing everything into one place. As a result, businesses experience fewer errors and smoother growth.
How Xorosoft ERP Ensures Inventory and Fulfillment Accuracy at Scale
Xorosoft ERP is purpose-built for high-growth businesses that can’t afford fulfillment mistakes. Instead of patching up errors after they happen, Xorosoft prevents them from occurring in the first place.
➡️ Real-Time Inventory Accuracy Across Every Location
With Xorosoft, your team has access to real-time inventory visibility across every warehouse and sales channel. Because the data is always live, your system knows exactly what’s in stock—no guesswork required.
As a result, customers only see what you can actually deliver. In turn, your brand earns more trust and fewer return requests.
➡️ Built-In WMS to Eliminate Human Errors
Unlike other platforms, Xorosoft’s Warehouse Management System (WMS) is fully integrated—not a bolt-on.
That means:
-
Scanning and picking workflows are guided by smart rules.
-
Orders are validated automatically before fulfillment begins.
-
Inventory updates in real time to reflect actual movement.
Consequently, warehouse teams make fewer mistakes, and shipping becomes predictable and fast. In addition, tracking becomes more accurate across departments.
➡️ Configurable Rules That Work for Your Business
Want to prevent shipping from the wrong warehouse? You can do that. Need to require approval for high-value orders? That’s easy too.
With Xorosoft’s custom rule engine, you can:
-
Block duplicate or suspicious orders
-
Validate addresses before shipping
-
Flag items on backorder
-
Restrict shipping methods for specific SKUs
These rules aren’t hardcoded. Instead, they’re fully configurable—without needing a developer. Because of this flexibility, your system adapts as your business grows.
How ERP Automation Supports Inventory Accuracy
One major source of fulfillment errors is poor integration. However, Xorosoft solves that with native connections to:
-
Amazon
-
EDI partners
-
3PLs and shipping carriers
Therefore, your data flows seamlessly from order to delivery. That means fewer delays, no double entry, and less chance of human error.
🔗 Explore our Shopify App Integration
Why Choosing the Right ERP Improves Fulfillment Accuracy
Xorosoft doesn’t just automate fulfillment—it gives you complete visibility.
You’ll be able to:
-
Automate invoicing, order updates, and returns
-
Set alerts for stockouts and late shipments
-
Monitor team performance and order accuracy in real time
📊 Want proof? Xorosoft is rated #1 in Ease of Use on G2. Users love the clean interface, flexible rules, and dependable automation.
Ready to Stop Mis-Shipments Before They Start?
Mis-shipments aren’t just fulfillment errors—they’re symptoms of deeper system issues.
When your ERP for inventory and fulfillment accuracy is working correctly, your team doesn’t have to fix errors. Instead, they prevent them.
Xorosoft helps you:
-
Centralize inventory and fulfillment workflows
-
Set up rules that prevent mistakes
-
Automate repetitive tasks across your tech stack
No more guessing. No more scrambling. Just control.
🚀 Ready to streamline fulfillment and eliminate errors?