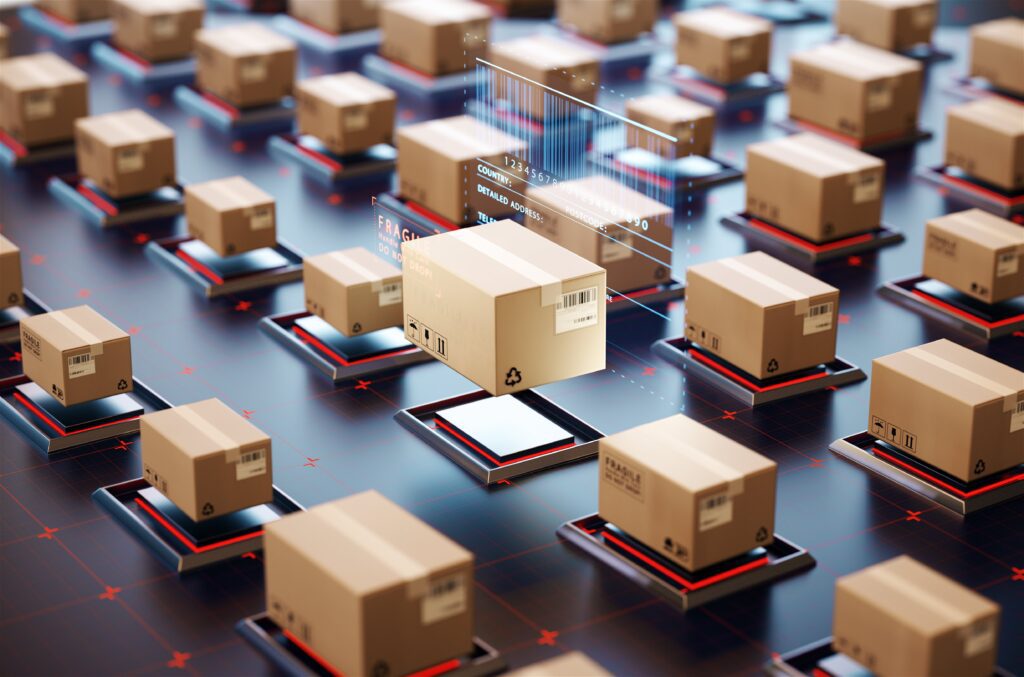
Introduction to Warehouse Management Systems (WMS)
Warehouse management is a critical aspect of any business that deals with inventory and storage. With the ever-increasing demands of the market, it has become essential for companies to implement an efficient system to manage their warehouses effectively. This is where a Warehouse Management System (WMS) comes into play. A WMS is a software application that helps businesses streamline their warehouse operations, improve efficiency, and enhance precision. In this comprehensive guide, we will explore the benefits of implementing a WMS, key features to look for, how to choose the right system for your business, the implementation process, best practices, and a case study of XoroWMS – a comprehensive WMS solution.
Benefits of Implementing a Warehouse Management System
Implementing a Warehouse Management System can bring numerous benefits to your business. One of the primary advantages is improved inventory accuracy. With a WMS, you can track your inventory in real-time, reducing the chances of stockouts or overstocking. This not only saves time and money but also improves customer satisfaction. A WMS also helps optimize warehouse space utilization by providing insights into the most efficient ways to store items. By organizing your inventory effectively, you can maximize your warehouse capacity and minimize wastage of space.
Another significant benefit of using a WMS is increased operational efficiency. Manual processes are prone to errors and can be time-consuming. By automating various warehouse tasks, such as order picking, packing, and shipping, a WMS can significantly reduce human errors and improve overall efficiency. This leads to faster order fulfillment, shorter lead times, and improved customer service. Additionally, a WMS provides better visibility into your warehouse operations, allowing you to identify bottlenecks and make informed decisions to optimize your processes.
Key Features of a Warehouse Management System
When choosing a Warehouse Management System for your business, it is essential to consider the key features that will best meet your requirements. Firstly, a WMS should have robust inventory management capabilities. This includes real-time tracking of inventory levels, stock allocation, and cycle counting. It should also have the ability to handle different types of inventory, such as raw materials, finished goods, and serialized items.
Another crucial feature to look for is order management. A WMS should enable efficient order processing, including order picking, packing, and shipping. It should support different order types, such as single orders, batch orders, and wave picking. The system should also have the flexibility to handle multiple shipping methods and integrate with various carriers for seamless order fulfillment.
Furthermore, a WMS should have comprehensive reporting and analytics capabilities. It should provide detailed insights into key performance indicators (KPIs) such as order accuracy, on-time delivery, and inventory turnover. This data is crucial for making informed decisions and continuously improving your warehouse operations. Integration capabilities with other systems, such as ERP and transportation management systems, are also essential to ensure smooth data flow across your organization.
Choosing the Right Warehouse Management System for Your Business
Selecting the right Warehouse Management System (WMS) for your business is a crucial decision that requires careful consideration. With numerous options available in the market, it is essential to evaluate your specific requirements and choose a system that aligns with your business goals. Here are some key factors to consider when choosing a WMS:
-
Scalability: Ensure that the WMS can scale with your business growth. It should have the capacity to handle increased order volumes, additional warehouses, and future expansion.
-
User-friendly Interface: Look for a system that is intuitive and easy to use. A user-friendly interface will reduce training time and improve user adoption across your organization.
-
Integration Capabilities: Consider the integration capabilities of the WMS with your existing systems, such as ERP and transportation management. Seamless integration ensures smooth data flow and eliminates manual data entry.
-
Customization Options: Assess whether the WMS can be customized to meet your specific business needs. A flexible system allows you to tailor workflows, reports, and processes to match your unique requirements.
-
Vendor Support and Training: Evaluate the level of support provided by the WMS vendor. Look for a vendor that offers comprehensive training, ongoing support, and regular system updates to ensure smooth operations.
By considering these factors and conducting thorough research, you can choose a Warehouse Management System that fits your business requirements and sets you up for long-term success.
Implementation Process of a Warehouse Management System
Implementing a Warehouse Management System (WMS) requires careful planning and execution to ensure a smooth transition. Here is a step-by-step implementation process to guide you:
-
Assessment and Planning: Begin by assessing your current warehouse processes and identifying areas that need improvement. Determine your goals and objectives for implementing a WMS. Create a project plan with timelines, milestones, and resource allocation.
-
System Configuration and Setup: Work closely with your WMS vendor to configure the system according to your specific requirements. This includes setting up inventory locations, defining workflows, and configuring order processing rules.
-
Data Migration: Transfer your existing inventory and customer data to the new WMS. Ensure data integrity and accuracy during the migration process. It is crucial to validate the data and perform thorough testing before going live.
-
Training and User Adoption: Conduct comprehensive training sessions for your warehouse staff to familiarize them with the new system. Encourage user adoption by highlighting the benefits and providing ongoing support during the transition period.
-
Pilot Testing and Evaluation: Run a pilot test of the WMS in a controlled environment to identify any issues or gaps. Gather feedback from users and make necessary adjustments before fully implementing the system.
-
Go-Live and Post-Implementation Support: Once the pilot testing is successful, implement the WMS across your entire warehouse operation. Monitor the system closely during the initial period and provide additional support to address any challenges or concerns.
By following this implementation process, you can ensure a successful deployment of your Warehouse Management System and start reaping the benefits of enhanced efficiency and precision.
Best Practices for Implementing a Warehouse Management System
Implementing a Warehouse Management System (WMS) can be a complex undertaking. To ensure a smooth and successful implementation, consider the following best practices:
-
Engage Key Stakeholders: Involve key stakeholders from different departments in the decision-making process. This ensures that the WMS aligns with the overall business strategy and receives buy-in from all relevant parties.
-
Thoroughly Train Users: Provide comprehensive training to all users of the WMS, including warehouse staff, supervisors, and managers. Training should cover all aspects of the system, including basic navigation, order processing, and reporting.
-
Start with a Pilot: Conduct a pilot test of the WMS in a controlled environment before implementing it across the entire warehouse operation. This allows you to identify any issues or challenges and make necessary adjustments.
-
Monitor and Measure Performance: Continuously monitor key performance indicators (KPIs) related to your warehouse operations. Track metrics such as order accuracy, on-time delivery, and inventory turnover to identify areas for improvement.
-
Regularly Review and Optimize Processes: Regularly review your warehouse processes and workflows to identify bottlenecks and areas for optimization. Leverage the reporting and analytics capabilities of the WMS to gain insights into your operations.
By following these best practices, you can ensure a successful implementation of your Warehouse Management System and maximize the benefits it brings to your business.
Key Features and Benefits of Xorosoft WMS
XoroWMS offers a host of key features that make it a powerful tool for warehouse management. Some of the standout features include:
-
Real-time Inventory Tracking: XoroWMS provides real-time visibility into inventory levels, allowing businesses to monitor stock levels accurately and prevent stockouts or overstocking.
-
Order Management and Fulfillment: The system streamlines order processing, from order picking to packing and shipping. It supports various order types, batch processing, and integration with multiple carriers for seamless order fulfillment.
-
Advanced Reporting and Analytics: XoroWMS offers comprehensive reporting and analytics capabilities, allowing businesses to track key performance indicators (KPIs), identify trends, and make data-driven decisions.
-
Integration with ERP and Other Systems: The WMS seamlessly integrates with existing ERP and transportation management systems, ensuring smooth data flow and eliminating manual data entry.
The benefits of implementing XoroWMS are numerous. Businesses can experience improved inventory accuracy, increased operational efficiency, faster order fulfillment, and enhanced customer satisfaction. Additionally, Xorosoft provides extensive training and support to ensure a smooth implementation and continued success.
How Xorosoft WMS Enhances Efficiency and Precision in Warehouse Operations
Xorosoft WMS is designed to enhance efficiency and precision in warehouse operations through its robust features and intuitive interface. By automating manual processes and providing real-time insights, Xorosoft WMS helps businesses optimize their warehouse workflows.
One way Xorosoft WMS enhances efficiency is through advanced picking strategies. The system enables wave picking, batch picking, and zone picking, reducing travel time and improving productivity. It also provides intelligent putaway suggestions, ensuring optimal utilization of warehouse space.
Furthermore, Xorosoft WMS improves precision by minimizing errors in order fulfillment. The system employs barcode scanning and RFID technology to ensure accurate picking, packing, and shipping. This eliminates picking errors and improves order accuracy, leading to higher customer satisfaction.
By leveraging the advanced features of Xorosoft WMS, businesses can achieve higher efficiency, greater precision, and improved overall performance in their warehouse operations.
Xorosoft WMS Training and Support
Xorosoft understands the importance of comprehensive training and ongoing support for a successful implementation of a Warehouse Management System. They provide extensive training programs tailored to the specific needs of their customers. These programs cover system navigation, configuration, reporting, and best practices for warehouse management.
In addition to training, Xorosoft offers dedicated support to their customers. Their support team is available to address any issues or concerns and provide timely resolutions. Xorosoft also provides regular system updates to ensure that businesses have access to the latest features and enhancements.
Conclusion
Implementing a Warehouse Management System (WMS) is a strategic decision that can significantly enhance efficiency and precision in your warehouse operations. By choosing the right WMS, following best practices, and leveraging the advanced features of the system, businesses can optimize their inventory management, streamline order processing, and improve overall performance.
XoroWMS, developed by Xorosoft, is a comprehensive WMS solution that offers a wide range of features and benefits. With real-time inventory tracking, advanced reporting and analytics, and seamless integration with existing systems, XoroWMS helps businesses achieve higher efficiency, greater precision, and improved customer satisfaction.
Book a demo with Xorosoft today to learn more about how XoroWMS can transform your warehouse operations and drive your business success.