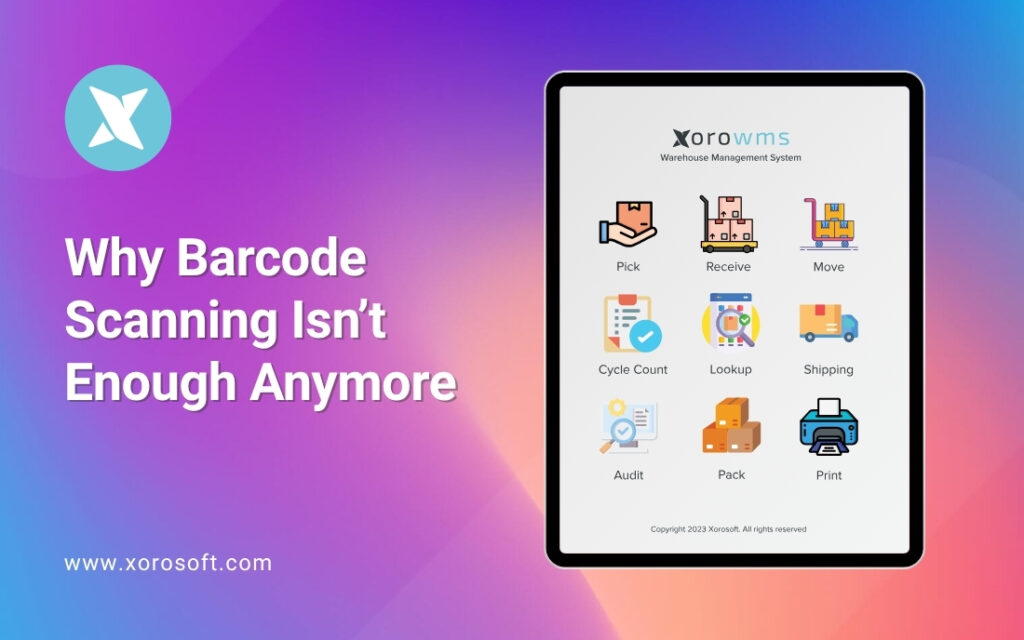
Barcode scanning limitations are holding your business back
Barcode scanning limitations are becoming a serious roadblock for growing businesses. What was once considered cutting-edge technology now holds operations back with inventory errors, fulfillment delays, and disconnected systems.
For years, barcode scanning was seen as a revolutionary tool for inventory control. It reduced human error, improved speed, and brought structure to fulfillment. However, that was then.
Today, barcode scanning limitations are showing up in costly ways—especially for fast-growing operations. If you’re running on barcode-only workflows, you’re probably already experiencing issues: stock inaccuracies, fulfillment delays, or data that doesn’t sync across systems.
Barcodes alone solved yesterday’s problems. But today, your business needs much more than basic scans to thrive.
What barcode-only workflows really cost you
Let’s break down the daily struggles of relying solely on barcodes:
-
Staff are scanning—but inventory levels are still wrong.
-
Orders are late because stockouts go unnoticed.
-
Pickers double-check scans, slowing down fulfillment.
-
Teams export reports into Excel just to make sense of the data.
-
When issues arise, tracing the root cause takes hours.
These aren’t small issues—they’re signals. Moreover, they reveal that your current system is lagging behind your business needs.
And it’s not the barcodes themselves. It’s the lack of system intelligence around them. A barcode can tell you what was scanned. However, it can’t tell you why something failed, who handled it, where it went wrong, or how to stop it from happening again.
Even worse, as your operations grow—more SKUs, more channels, more warehouses—this fragility only gets amplified. Therefore, what worked when you were shipping 50 orders a day starts breaking at 500.
The deeper issue: why barcode scanning fails to scale
Barcode scanning limitations come from more than just outdated technology. Let’s explore where it breaks down:
1. Barcodes lack operational context
A scan gives you a single data point. However, without knowing where the item is, what its status is, or how it fits into the larger fulfillment process, you can’t act on it intelligently.
2. No real-time visibility
Legacy systems that rely on batch updates can’t support live decision-making. As a result, teams often operate with outdated or incomplete data.
3. Manual processes persist
Even with barcode scanners, tasks like reordering, reporting, and fulfillment planning are often manual. Consequently, this slows down operations and introduces error.
4. Tools don’t talk to each other
Scanners may work fine, but they often don’t integrate well with Shopify, shipping tools, or accounting software. In turn, data stays siloed and disconnected.
5. Scalability is limited
Throwing more scanners at a problem doesn’t fix process breakdowns. Instead, without a unified system behind them, barcode-only operations become chaotic fast.
In short, barcodes capture actions—but not meaning. And meaning is what helps you grow. In comparison, a unified ERP system provides decision-making support beyond transactional data.
The shift to real-time, connected intelligence
Modern operations require much more than barcode scans. They need a unified view across inventory, orders, fulfillment, and financials—updated in real time and accessible to the entire team.
Here’s what today’s leaders need:
-
Live visibility into every SKU across locations
-
Awareness of reserved, in-transit, or returned inventory
-
Full traceability of who did what, when, and where
-
Instant insights into operational bottlenecks
-
Data that ties warehouse movements to business outcomes
That level of control simply isn’t possible with disconnected barcode tools. Therefore, businesses are now turning to centralized ERP systems to bridge the gaps. Furthermore, connected systems reduce human dependency and improve accuracy dramatically.
Barcode scanning limitations are why ERP is essential
Scanners capture “what” moved. But ERPs help you understand “why,” “how,” and “what’s next.” Consequently, this enables you to fix problems before they happen again.
That’s why growing teams are moving to unified platforms like Xorosoft ERP, where barcode data powers real-time automation and decision-making—not just records activity.
Let’s explore how it works. For instance, what if a scan could automatically trigger a shipment, update accounting, and reorder stock? With Xorosoft, it can.
How Xorosoft ERP removes barcode scanning limitations
Xorosoft is designed for scaling businesses outgrowing spreadsheets, QuickBooks, and basic barcode systems. It replaces disconnected tools with a single, cloud-based ERP platform—one that gives you full visibility, control, and automation.
Here’s how Xorosoft redefines operations:
🔍 Real-time inventory control
With Xorosoft, inventory is updated the moment it moves—across every warehouse, store, or 3PL. As a result, you’ll always know what’s available, what’s committed, and what’s expected in real time.
No need to cross-check spreadsheets. No more stock surprises. Instead, your team can act instantly with full confidence in the data.
📦 Native WMS with smart scanning
Unlike other systems that add WMS as a plugin, Xorosoft includes a fully integrated warehouse management system. It supports wave picking, bin tracking, putaway rules, cycle counting, and more.
Therefore, barcodes become triggers for smart workflows—not just data entry. Additionally, this improves warehouse productivity from day one.
🔄 Seamless integrations with Shopify, Amazon, and more
Your barcode scans instantly update across Shopify, Amazon, EDI, and your accounting system. There’s no lag, no manual syncing, and no missed steps. In fact, it feels as though every platform is working as one.
👉 Xorosoft on Shopify App Store
🧠 Custom automation and alerts
Set up rules to auto-reorder, notify teams, or trigger workflows based on scans, inventory thresholds, or order types. This way, you’re no longer reacting to problems—you’re preventing them. Meanwhile, your system continues running in the background, handling complexity without bottlenecks.
📈 Full audit trails and reporting
Every scan, order, and adjustment is logged with user stamps and timestamps. To clarify, that means every action is traceable and accountable. This is especially useful during audits or inventory reconciliation.
🏆 User-friendly and ranked #1 on G2
Ease of use matters. Xorosoft is ranked #1 in Ease of Use on G2 and is a High Performer in the ERP category. Therefore, it’s built for rapid deployment, easy adoption, and fast results. Even so, it’s robust enough to handle multi-location complexity with ease.
Ready to move beyond barcode-only chaos?
Barcode scanning was once a competitive advantage. Today, it’s just the baseline.
To compete, you need a system that goes further—connecting every scan to meaningful insights, automating tasks before they become bottlenecks, and giving your team full control.
Xorosoft ERP transforms scanning into strategy. It bridges warehouse activity with inventory intelligence, order fulfillment, and financial reporting—all in one place.
👉 Book your demo today and experience the ERP that removes barcode limitations for good.
Search
Categories
- ACCOUNTING & FINANCIALS 39
- Business 1
- E-COMMERCE & CHANNEL INTEGRATIONS 48
- ECommerce 3
- ERP 701
- FINANCE & ACCOUNTING 9
- INVENTORY & OPERATIONS 11
- Inventory Management Software 1
- OPERATIONS & INVENTORY 39
- PROCUREMENT & SUPPLY CHAIN 9
- PURCHASING & SUPPLY CHAIN 40
- Software 1
- WAREHOUSE & FULFILLMENT WMS 41
- WMS & FULFILLMENT 12
Recent Posts
-
One Missed Order Window. One Season Wasted. Don’t Risk It.
-
Modern Warehousing Isn’t Just About Speed—It’s About System Clarity
-
Your Finance Team Deserves Better Tools Than Band-Aids
-
The ‘Spreadsheet Trap’ That Keeps Ops Teams in the Dark
-
Selling Everywhere Is Easy—Managing It Isn’t (Unless You Have This)