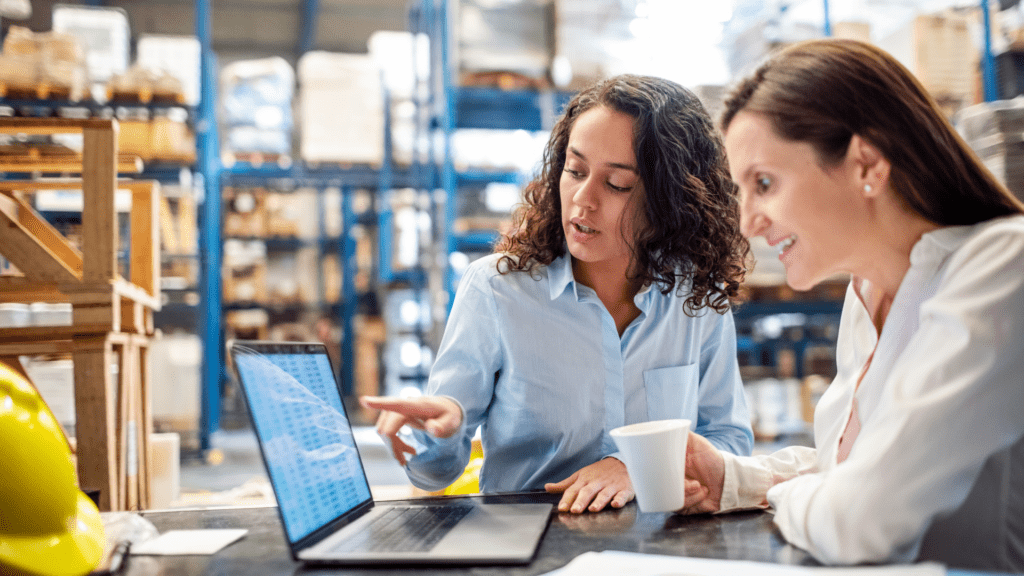
Inventory management is an important part of any business. It is important to monitor inventory levels and ensure that all orders are fulfilled in a timely and efficient manner. To do this, companies must use key performance indicators (KPIs) to measure the performance of their inventory management systems. Key performance indicators (KPIs) are essential tools for measuring the performance of any organization. KPIs provide valuable insights into the health of an organization and help to inform strategic decision-making. They help to identify areas of improvement and highlight strengths and weaknesses. In this article, we will take a look at 20 Essential KPIs for Streamlined Inventory Management.
20 Essential KPIs for Streamlined Inventory Management
1. Inventory Turnover Ratio: This KPI measures the speed at which a company is selling its inventory and replacing it with new inventory. It is calculated by dividing the cost of goods sold by the average inventory. A higher inventory turnover ratio indicates that the company is efficiently selling its inventory and replacing it with new inventory.
Inventory Turnover Ratio = Cost of Goods Sold/Average Inventory
2. Order Fulfillment Cycle Time: This KPI measures the time it takes from when an order is placed with a supplier to when the customer receives the order. It is calculated by adding the lead time, shipping time, and receiving time together. A lower order fulfillment cycle time indicates that the order is being fulfilled quickly and efficiently.
3. Inventory Accuracy: This KPI measures the accuracy of the inventory records. It is calculated by dividing the actual inventory count by the ideal inventory count, and then multiplying that number by 100. A higher inventory accuracy indicates that the inventory records are accurate and up-to-date.
Inventory Accuracy = (Actual Inventory Count/Ideal Inventory Count) x 100
4. Inventory Obsolescence: This KPI measures the value of inventory that is no longer usable. It is calculated by dividing the obsolescence value by the ideal inventory value, and then multiplying that number by 100. A higher inventory obsolescence indicates that more inventory is becoming unusable.
Inventory Obsolescence = (Obsolescence Value/Ideal Inventory Value) x 100
5. Stockout Rate: This KPI measures the rate of orders that are not filled due to lack of inventory. It is calculated by dividing the number of stockouts by the total orders, and then multiplying that number by 100. A higher stockout rate indicates that the company is not able to fulfill customer orders due to a lack of inventory.
6. Stockout Cost: This KPI measures the cost associated with stockouts. It is calculated by dividing the cost of stockouts by the total number of stockouts. A higher stockout cost indicates that the company is incurring more costs due to lack of inventory.
7. Inventory Carrying Cost: This KPI measures the cost associated with holding inventory. It is calculated by dividing the inventory carrying cost by the average inventory value, and then multiplying that number by 100. A higher inventory carrying cost indicates that the company is incurring more costs due to holding inventory.
8. Inventory Availability: This KPI measures the rate of inventory available to fulfill orders. It is calculated by dividing the available inventory by the total inventory, and then multiplying that number by 100. A higher inventory availability indicates that the company has more inventory available to fulfill orders.
9. Safety Stock Level: This KPI measures the amount of inventory needed to maintain a desired service level. It is calculated by multiplying the lead time by the average demand, and then dividing that number by (1-desired service level). A higher safety stock level indicates that the company has more inventory on hand to maintain a desired service level.
10. Reorder Point: This KPI measures the amount of inventory needed to place a new order. It is calculated by adding the safety stock level and the (order lead time x average demand). A higher reorder point indicates that the company needs more inventory to place a new order.
11. Economic Order Quantity: This KPI measures the optimal amount to order in order to minimize total cost. It is calculated by taking the square root of (2AS/C), where A is the annual usage of the item, S is the cost of placing an order, and C is the cost of holding an item in inventory. A higher economic order quantity indicates that the company is ordering the optimal amount of inventory in order to minimize costs.
12. Average Lead Time: This KPI measures the average time it takes from when an order is placed to when the inventory is received. It is calculated by dividing the total lead time by the number of orders. A lower average lead time indicates that the order is being received faster.
13. On-Time Delivery Rate: This KPI measures the rate of orders that are delivered on time. It is calculated by dividing the number of on-time deliveries by the total number of deliveries, and then multiplying that number by 100. A higher on-time delivery rate indicates that the company is delivering orders on time.
14. Backorder Rate: This KPI measures the rate of orders that cannot be fulfilled due to lack of inventory. It is calculated by dividing the number of backorders by the total number of orders, and then multiplying that number by 100. A higher backorder rate indicates that the company is unable to fulfill customer orders due to a lack of inventory.
15. Inventory Replenishment Frequency: This KPI measures the rate of inventory replenishments. It is calculated by dividing the total number of replenishments by the total inventory. A higher inventory replenishment frequency indicates that the company is replenishing inventory more often.
16. Inventory Utilization Rate: This KPI measures the rate of inventory that is used. It is calculated by dividing the used inventory by the total inventory, and then multiplying that number by 100. A higher inventory utilization rate indicates that the company is using more of its inventory.
17. Lost Sales Rate: This KPI measures the rate of sales lost due to lack of inventory. It is calculated by dividing the number of lost sales by the total number of sales, and then multiplying that number by 100. A higher lost sales rate indicates that the company is losing more sales due to lack of inventory.
18. Fill Rate: This KPI measures the rate of orders that are filled. It is calculated by dividing the number of orders filled by the total number of orders, and then multiplying that number by 100. A higher fill rate indicates that the company is able to fill more customer orders.
19. Days of Supply: This KPI measures the amount of inventory on hand relative to the average daily usage. It is calculated by dividing the average inventory by the average daily usage, and then multiplying that number by the number of days. A higher days of supply indicates that the company has more inventory on hand relative to the average daily usage.
20. Inventory Shrinkage Rate: This KPI measures the rate of inventory lost due to theft, damage, or other causes. It is calculated by dividing the inventory shrinkage by the total inventory value, and then multiplying that number by 100. A higher inventory shrinkage rate indicates that the company is losing more inventory due to theft, damage, or other causes.
Conclusion
Businesses of any nature (Retail, Wholesale, or ECommerce) need to stay on top of their inventory KPIs in order to ensure that their operations are running efficiently and effectively and that they are meeting their business objectives. By tracking and analyzing these KPIs, businesses can identify areas of improvement and make adjustments as needed. Tracking and analyzing these KPIs can also help businesses to reduce costs and increase profits by optimizing their inventory management strategies
Additionally, An ERP (enterprise resource planning) system like Xorosoft can provide real-time data on inventory levels, order fulfillment times, shipping times, and other factors that can help to accurately measure and analyze these KPIs. An ERP system can also automate the process of tracking and analyzing KPIs, which can save time and reduce costs.